

Midwest Territory Manager
Stefin Sobel has dedicated his career to the waste and recycling processing industry for over 30 years. During this time, he has gained extensive experience working with heavy recycling, baling and compaction equipment, as well as haulage, transfer and various other aspects of the industry.
1. How do I determine the right kind of slow-speed shredder for my business application?
Choosing the correct slow-speed shredder starts with the type of materials you intend to process. For materials like green waste, wood waste, biomass, paper, plastics and bulky waste, a single-shaft shredder is the leading choice. For more difficult materials, such as tires, construction and demolition (C&D) waste, white goods, light metals and municipal waste, a dual-shaft, low-speed shredder is your best bet.
2. What’s the difference between single- and double-shaft shredders?
Single-shaft shredders are well known for their reliably high throughput and consistent material fraction varieties, depending on the sizing screen choices a customer makes. Dual-shaft shredders, with their slower speeds and high torque, make easy work of the most difficult materials like C&D waste.
You may ask yourself, “Why not just get the dual-shaft shredder to process everything?” The simple answer is throughput. Although a dual-shaft shredder can handle easy to difficult-to-shred materials, a single-shaft shredder’s throughput is typically twice that of a dual-shaft shredder.
3. How do you customize a shredder for different shred sizes and throughput?
There are a variety of ways a customer can customize both a dual-shaft and a single-shaft shredder to create fractions ranging from 2 inches to 24 inches. The dual-shaft shredders accomplish this task with the use of “breaker bars.”
These bars are designed in a variety of styles, from “flat bar,” which is used to create the largest fraction sizes, to “basket bar,” which is designed to create the smallest fraction sizes and pretty much everything in between. Single-shaft shredders use “sizing screens” to fractionate materials. These screens are installed around and under the shaft. Sizing screens only allow materials small enough to pass through them to eject from the working chamber which creates a very homogenous material fraction.
4. Is it possible to get a machine of this size quickly? How far in advance should I plan?
Pronar is a vertically integrated manufacturer, which means they design and manufacture about 90 percent of the components used in every machine. This means that we have not experienced some of the supply chain issues that are plaguing many global industries. We are proud to say that we have more than 20 slow-speed shredders in inventory with more on the way in the next coming weeks and months. We’re able to make immediate deliveries on most dual-shaft and single-shaft shredders, as well as trommel screens and mobile stacking conveyors.
5. What kind of maintenance is required for a shredder, and how would you keep it on track in the field?
All Pronar shredders come standard with an industry-leading 24-month/1,500-hour parts and labor warranty. This warranty, coupled with our standard telematics maintenance system, allows you to remotely monitor your shredder from anywhere. Check your machine hours, fuel levels and hydraulic temperatures and set alarms for routine maintenance right from your phone, laptop or desktop computer.

It doesn’t stop there, our dedicated service team is monitoring and advancing their skills on a variety of important machine functions and features. This allows them to easily diagnose and repair simple issues before they turn into larger ones.
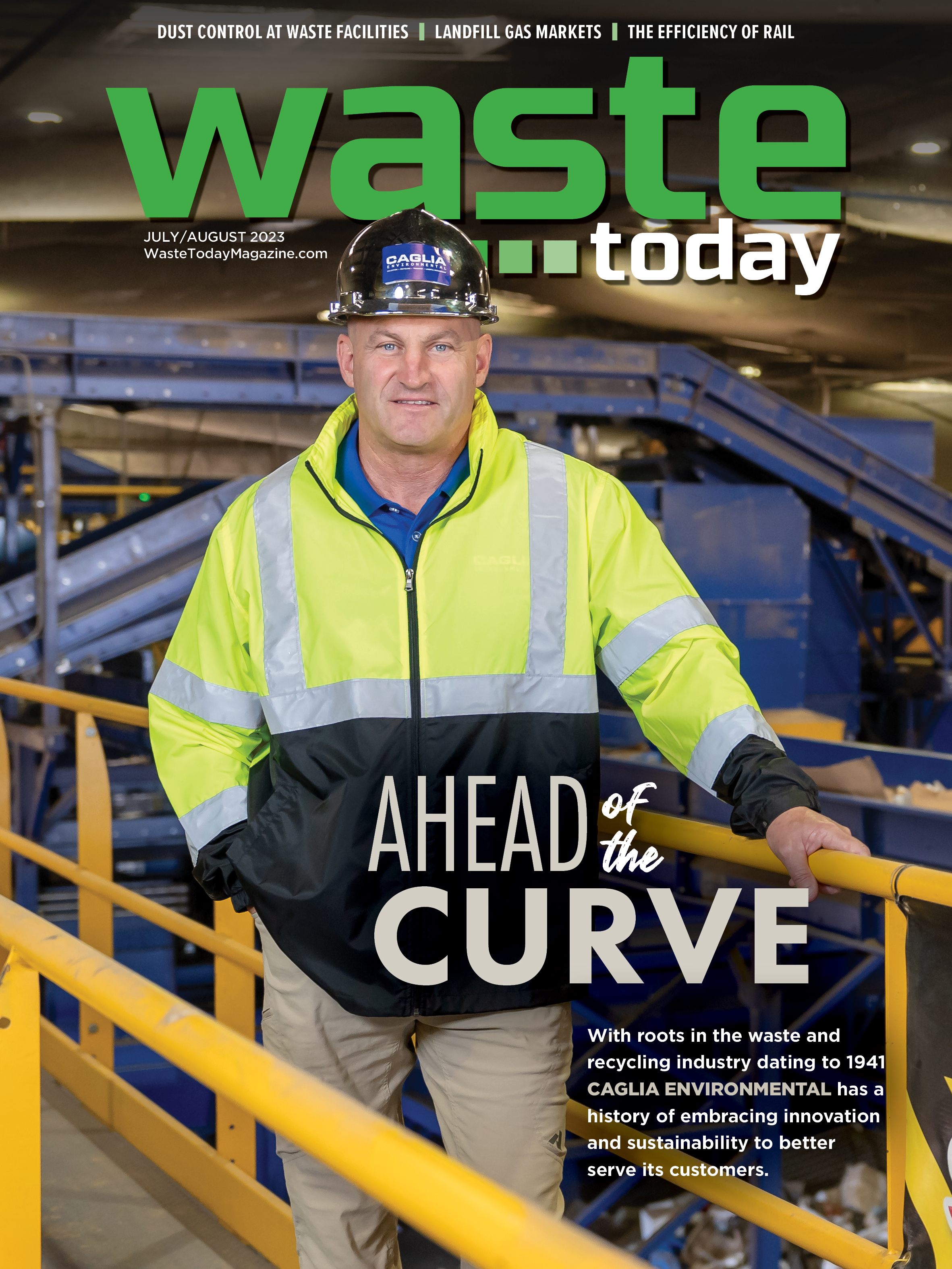
Explore the July August 2023 Issue
Check out more from this issue and find your next story to read.