
When it comes to reduction equipment, construction and demolition (C&D) recyclers have a plethora to choose from. From shredders and chippers to tub and horizontal grinders, a variety of machines exist to whittle C&D wood down to bits that can be turned back into useful end products.
But with so many options, including variations within each make and model of machine, choosing the right one can be complex. By evaluating the needs of an operation beforehand, though, operators can make the right choice when it comes time to purchase.
Finding the right fit
When deciding what type of reduction equipment to purchase, operators must first consider two things: the primary material going in and the ideal material coming out. Chippers and shredders are typically used in the first phase of processing, while grinders are often used to further refine material into marketable products.
“Some of the big questions operators have to ask themselves are, ‘What is 95 percent of your material going to be when you're processing? What’s the size of it, what’s the density of it, what are the contaminants in it?’” says Jody Parker, a regional sales manager for Rotochopper, based in St. Martin, Minnesota. “And then, the secondary component to that is, what is it you’re trying to make?”
Chippers are best for quickly processing clean logs and small round wood into chips and sawdust. These are ideal for processing a steady stream of homogenous raw wood into chips for particle board, pellet fuel, paper and pulp and other applications.
Shredders are mainly used to process commingled, contaminated waste streams like municipal solid waste and synthetic materials that are difficult to break apart, like carpet. These machines are typically used to pre-process raw contaminated waste streams and often can’t produce a quality end product.
That is where grinders come in. As perhaps the most versatile piece of reduction equipment, grinders can handle a variety of materials, including logs, whole trees, brush, forestry residue, sorted pallets, waste, agricultural products and shingles. They can also create a variety of end products, including chips, colored mulch, playground cushion, fine-texture fiber and compost.
Grinders also can handle mixed C&D streams with some contamination, depending on the size of their screens. Parker says when dealing with highly contaminated streams, though, they are best used in a second pass to refine material that has already been broken up. Manually picking and batch sorting methods are also effective before passing material through a grinder.
“In a grinder, you can get a really big screen just to bust the material up and try to liberate steel, even liberate rock—anything that might, with a smaller screen, roll around in the grinding chamber longer and create more damage and more wear. Anything you can do to liberate that kind of stuff is beneficial,” Parker says. “In a slow-speed shredder, pulling that material apart and really ripping out the larger pieces of steel is really helpful.”
When it comes to grinders, two main models exist on the market: tub and horizontal.
While tub grinders were once the industry standard, Lars Bergan, another regional sales manager for Rotochopper, says “you now see very few tub grinders in [the C&D] space because they’re not safe.” Since the rotor is exposed at the bottom of the tub in these machines, objects are more susceptible to hurling out of the top, Bergan explains.
Horizontal grinders also have the potential to throw objects, but because the feed openings are smaller, the risk is less than that of tub grinders.
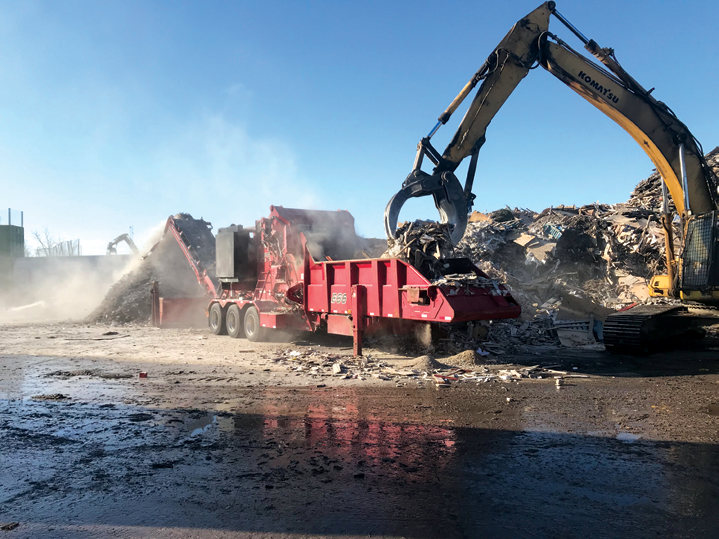
Size, weight and speed
If an operator determines that a horizontal grinder is best suited for his or her needs, the next consideration for choosing the right machine should be the size and weight of the material that will be processed.
Horizontal grinders come in sizes that vary both by their throat opening and by their overall body.
“Basically, the bigger and heavier the wood you’re grinding, the more horsepower and the bigger grinder you want to have,” Bergan says. “Volume plays a role, too. Even if you’re doing smaller material or green waste, but you need to do massive volume, then you’re still going to need a bigger machine. So, it really depends a lot on how you plan on using it.”
The right-sized grinder depends on the material being processed and where it will be placed. Before purchasing a grinder, users should consider whether it will be mobile or fixed. If it will be used in mobile applications, users should make sure it can be transported on all roads it will be trailered to; if fixed, operators need to carefully measure the space it will occupy to ensure it will fit.
“If you’re building something new and can build around the grinder you pick, all the better, but often that’s not the case and people need to fit it into a particular spot,” Bergan says.
In addition to size and weight considerations of the material that need to be assessed, it is important for users to think about the speed with which they’ll process the material. Typically, the more horsepower the machine has, the larger the rotor and powerfeed drum tend to be.
Some processors use grinders as part of a conveying system that constantly feeds material to the machine. Others use grinders only for a couple hours at the end of each day when material has been picked through and preprocessed.
“[The decision] depends not only on how much material you have, but also on how quickly you want to get the job done,” Bergan says.
Diesel vs. electric
Horizontal grinders can be powered by two sources: diesel fuel and electricity.
The more modern electric grinders offer several advantages over diesel, Bergan says.
“The advantage to electric is generally lower energy costs, they’re generally less expensive to buy, they're much quieter and require much less maintenance,” Bergan says. “There are no radiators, no filters or oil changes—all the stuff that goes into having a diesel engine, you don’t have any of that.”
Deciding between the two can come down to where the owner intends to use the grinder. Electric machines are more easily incorporated into conveyor systems, and they don’t present indoor gas emission concerns like diesel-powered grinders do. However, diesel grinders can come in handy in certain outdoor applications. For example, in a mulch yard where wood waste processing is needed in several areas, diesel machines can be moved to different piles of debris instead of having to move the machine to one central location.
“The advantage to diesel is more mobility,” Bergan says. “You can use them in many different places, and they’re easy to move around.”
Other considerations
Along with the aforementioned considerations, several other variables exist among grinders that need to be taken into account before making a purchase.
Grinders require regular upkeep and maintenance, especially on their screens and teeth, which are susceptible to wear and tear. Discharge belts also need to remain tightened to avoid wear. Damage can be reduced by avoiding contaminants, so users should implement a comprehensive presort process, if applicable.
Using the different types of teeth available for grinders can also help users reduce wear, depending on the material they’re handling. Teeth come in several variations for different applications, so choosing the right ones and configuring them appropriately for the specific operation will also cut back on wear and tear.
“I think the flexibility of a grinder is what sets it apart,” Parker says. “The ability to change all those types of teeth and screen sizes so that you can create a bulkier material or a shredded material or a chipping material—it just gives people who are trying to make a different type of finished product, or who are trying to handle different types of incoming material, more options.”
This article originally ran in the September-October issue of Construction & Demolition Recycling magazine. The author is the assistant editor for Construction & Demolition Recycling and can be contacted at tcottom@gie.net.
Latest from Waste Today
- US Composting Council grant will fund data collection
- Enviri releases annual ESG report
- Waste Connections enjoys income, revenue boosts
- Machinex recognized as Recycling Equipment Innovator of the year
- WM announces solid Q2 growth
- Reworld partners with Genpact
- Waste Pro earns favorable financing rating
- Amberjack announces exit from investment in Best Trash