
Since the recycling industry adopted them in the ‘90s, the role of optical sorters in material recovery facilities (MRFs) has grown dramatically. What was once reserved for certain types of plastic sorting applications has now expanded to fiber, glass, cartons and organics, as well as to e-scrap and construction and demolition recycling applications.
Advancements in processing power, flexibility and accuracy have made optical sorters an appealing option for MRF operators.
“Optical sorters, in general, are a great asset in a MRF because they are accurate and can do a lot of the heavy lifting, making the job of the sorters much easier,” says Carlos Batista, MRF operations manager at Mazza Recycling, Tinton Falls, New Jersey.
Evolution in efficiency
One of the main changes to optical sorters has been their computing power. For example, the machines’ improved data processing allows operators to get better information from the material, improving accuracy. The machines’ optics also have improved, which means they can spot objects more quickly and more clearly to better sort.
“They’re making leaps and bounds from when they started,” says Jim Marcinko, recycling operations director for WM, Houston. “They became much more robust to deal with the solid waste environment.”
Marcinko says optical sorters’ durability has increased, and they are easier to maintain than in the past, as well. When they first started being used in MRFs, factors like dust and vibration affected how the sorters worked because they initially were designed for use in food processing. Now, Marcinko says, sorters can go between one to three months without needing to be recalibrated.
He adds that when WM originally began using optical sorters in the early 2000s, they generally sorted plastic containers. Now, the company uses them to sort different paper, cardboard fibers and plastic films, Marcinko says, adding that the equipment also is good at performing quality control for various material streams.
“Before, they were 3 feet wide; now you can get them up to 10 feet wide, so you can do a lot more things with them where we would not have before, like on fiber lines, where there was too much material to be optically sorted.”
Batista says the five optical sorters Mazza Recycling installed in 2020 sort mixed paper and plastics, such as polyethylene terephthalate (PET), polypropylene and high-density polyethylene (HDPE). Mazza’s Tinton Falls facility uses two optical sorters on the paper line and three on the container line to sort plastics.
Whether optical sorters positively or negatively sort materials depends on their placement in the MRF and the performance the operator wants to achieve, say Batista and Marcinko.
“It depends on the volume of material going in it,” Marcinko says. “If it’s something that you need very pure that has a reasonable amount of volume, you may want to use it as a positive sort [of a material], like a PET.”
Both operators say that if the sorter is being used on the paper line, it might make more sense to remove objects from the paper stream because of the volume of the fiber involved.
Optimizing performance
One of the primary factors that affect the performance of an optical sorter is its size and where it is placed in the overall design of the MRF. Marcinko says the size of the sorters also will affect the layout of the MRF and the size of the conveyors needed.
“Depending on how many sorters you have in sequence, it creates a lot of transitions, which require more space to account for,” he says.
Batista says the degree of contamination and the moisture level of the material can affect optical sorter performance.
When the optical sorter fires on a desired object, an overlapping, different object also could be ejected, leading to cross-contamination in the sorted material stream.
To keep optical sorters working at peak performance, it is important to perform standard maintenance. This includes cleaning the sensor windows and testing the air valves daily. Operators also should monitor and, if required, adjust the tracking of the high-speed acceleration conveyor belt, its bearings and areas around and below the return idlers, tail and head pulleys.
With a declining volume of newspaper and a higher percentage of cardboard in the fiber stream, optical sorters that perform quality control sorting must constantly be monitored and possibly adjusted. On the container side, the increase of bottles with full-sleeve labels made with a variety of label resins has made it necessary to adjust optical sorters accordingly. The reference library containing the different material and color categories should be updated to maximize the recovery of plastic containers, in general, and PET containers in particular, Felix Hottenstein, sales director at MSS Optical Sorters, wrote in an earlier article for Waste Today.
Before acquiring an optical sorter, which costs between $330,000 and $500,000, experts advise operators to speak with a preferred supplier about what optical sorters best fit the task. They also should tour a MRF that incorporates a machine they’re considering to see how it works and to talk to the operators.
Marcinko says businesses need to consider the costs and benefits before acquiring optical sorters. In that analysis, MRF operators should weigh the cost and effectiveness of an optical sorter compared with hand sorting.
Batista adds that a company needs to understand the type of materials the MRF receives and how they change seasonally.
“I would definitely make sure that you do your research and make sure that you know the direction that you want the machine to sort,” Batista says.
Labor saving alternative
In light of hiring difficulties, experts believe the role of optical sorters at MRFs will only grow.
WM says it plans additional investments in optical technology as a solution to the hiring issue. James Fish, president of WM, during the company’s first-quarter 2022 conference call held April 26, said WM anticipates reducing 5,000 to 7,000 positions over the next four years. He added that in this tight job market, it makes sense to use technology to reduce dependency on certain high-turnover jobs such as sorters.
The need for education in the community has decreased, Batista says, because these sorters can pick out and prevent contamination at a more efficient rate than manual sorters can.
While WM is expanding its use of technology, Marcinko says he doubts the industry will develop new roles for optical sorters.
“I don’t know if it’ll continue to grow because I think it’s kind of everywhere it can be right now within the facility,” he says. “As other streams of material come along … if there are new types of plastics that are developed, it may grow. But these machines are very capable. I just have a hard time seeing what more they need to do.”
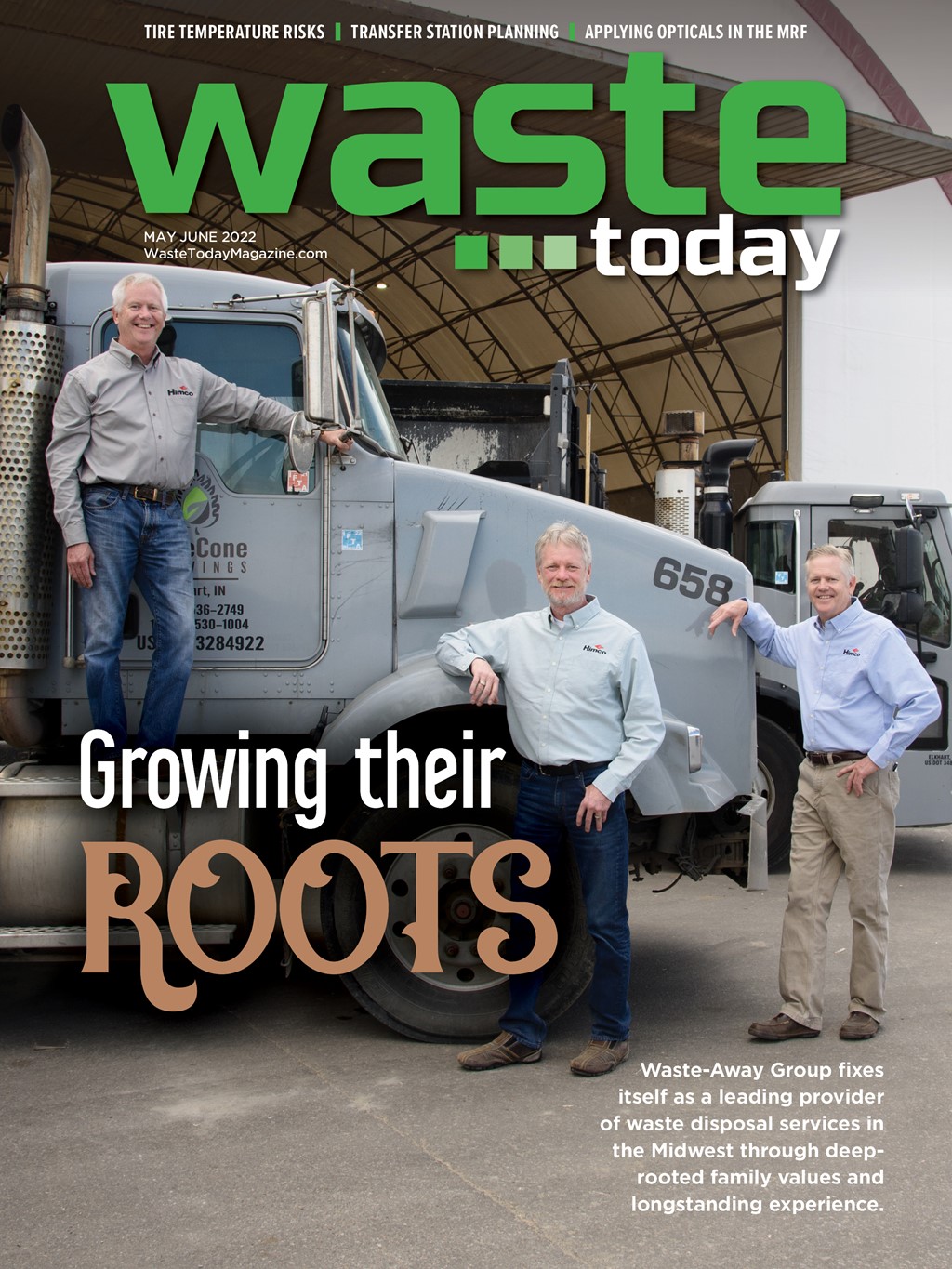
Explore the May June 2022 Issue
Check out more from this issue and find you next story to read.
Latest from Waste Today
- Washington implements methane reduction regulations for landfills
- Fuzion announces water recycling initiative
- Sustainable Green Team and Revive Terra set to merge
- WPWMA hires agency’s first general manager
- Stellar adds to sales staff
- Amos Manufacturing part of battery recycling technology effort
- Waga adds North Carolina landfill to its project list
- Recycling-related companies among export honorees