
Last year, efforts to develop innovative technologies and facilities designed to divert more nonrecyclable waste away from landfills produced a mixed bag of results. It calls to mind the classic refrain: two steps forward, one step back.
Early in the year, the Wasatch Integrated Solid Waste Management District in Davis County, Utah, announced it would close its resource recovery facility. Over its 30 years in operation, this facility diverted over 3.7 million tons per year of nonrecyclable municipal solid waste (MSW) away from the district’s landfill, converting it into renewable steam for nearby Hill Air Force Base. Last year, the Air Force decided to switch its steam supplies away from this renewable energy source in favor of total reliance on low-priced natural gas-fueled energy production, rendering the Wasatch resource recovery facility uneconomic. The facility closed in May 2017, resulting in the loss of 30 jobs, but the district has a plan. The district will develop a new facility, converting MSW into an engineered alternative fuel for use at a nearby cement kiln and an organic feedstock for anaerobic digestion at a nearby wastewater treatment facility.
The engineered alternative fuel technology is one in which we see growing interest in the U.S. This technology is already widely used in Europe, where its greenhouse gas (GHG) reduction value can be monetized. This past year, Entsorga North America, Wilmington, North Carolina, continued in the construction of a 500-ton-per-day facility in Berkeley County, West Virginia. In December 2017, RePower South, Spartanburg, South Carolina, completed the bond financing for a 600-ton-per-day alternative fuel facility. In these projects, the target fuel consumer is typically cement kilns.
There are better ways to manage nonrecyclable waste than burying it—a great New Year’s resolution for 2018 and beyond.
A significant waste management industry development last year was China’s new policies affecting the importation of waste-derived recyclables. China’s waste ban has taken effect, but the impacts are still unknown. The central question remains: Will there be a viable market for low-quality materials such as mixed paper? A group of communities in Maine isn’t waiting to find out. Known as the Municipal Review Community, or MRC, the group is moving forward with a 600-ton-per-day advanced mechanical biological treatment (MBT) facility, which is being built, owned and operated by Fiberight LLC, Catonsville, Maryland.
This technology is designed to recover not only traditional high-value recyclables from a mixed waste stream, but also low-quality fibers which today are considered nonrecyclable. It will also convert food waste, one of the largest components of MSW, into renewable natural gas. Construction of the Fiberight facility began in 2017 and commercial operations are expected to commence in the second quarter of 2018. Sadly, the opening of the new Fiberight facility may result in the closure of another old conversion facility, the 1,000-ton-per-day Penobscot Energy Recovery Company (PERC) in Orrington, Maine. The PERC facility faithfully served the needs of the MRC communities for over 30 years, but again, today’s relatively low energy values have rendered it uneconomic.
I believe it is noteworthy that communities and leaders who were visionaries 30 years ago with the development of their resource recovery facilities, like the MRC and Wasatch, are once again on the forefront in the development of facilities utilizing innovative technology to divert their nonrecyclable waste from landfills. The leaders of these communities are putting into practice what we all know: There are better ways to manage nonrecyclable waste than burying it—a great New Year’s resolution for 2018 and beyond.
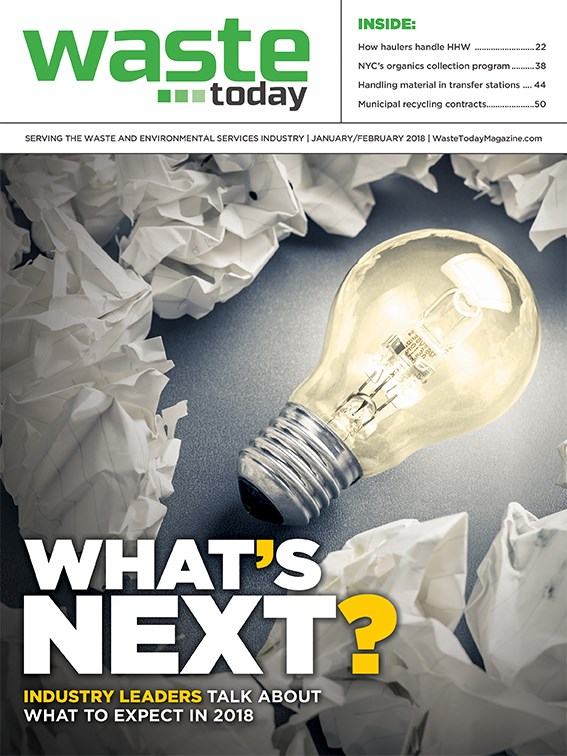
Explore the January February 2018 Issue
Check out more from this issue and find your next story to read.
Latest from Waste Today
- US Composting Council grant will fund data collection
- Enviri releases annual ESG report
- Waste Connections enjoys income, revenue boosts
- Machinex recognized as Recycling Equipment Innovator of the year
- WM announces solid Q2 growth
- Reworld partners with Genpact
- Waste Pro earns favorable financing rating
- Amberjack announces exit from investment in Best Trash