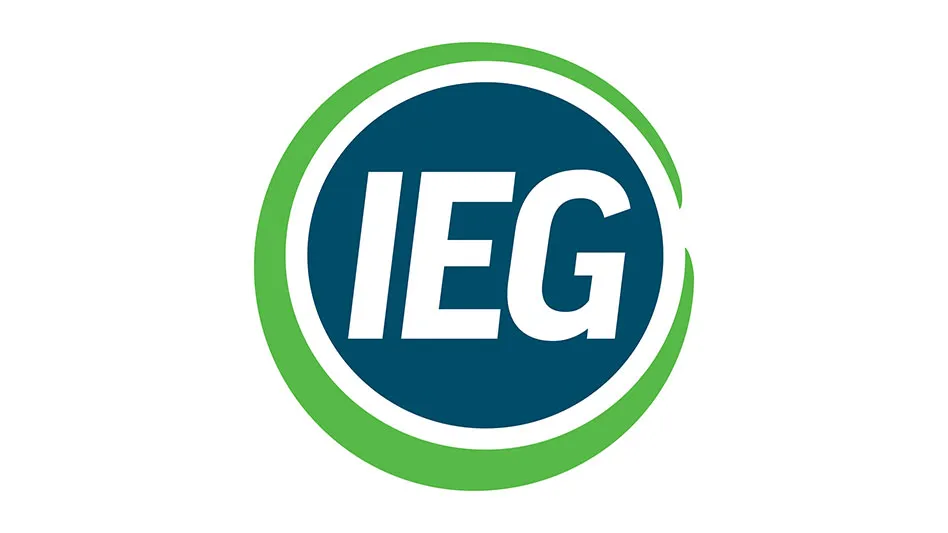

The evolution of commercial container repair has primarily been driven by the economics of extending the life of a container versus the cost of purchasing a new asset. The emphasis on repair versus replace also has grown with the industry’s commitment to sustainability. While several parts of a container can fail over time, the most common repair is replacing a corroded bottom. It’s no surprise that the bottom of the container is its Achilles’ heel as it’s the final destination for most liquid waste and stormwater. Over time, steel and moisture do not play well together. Replacing a rusted container bottom is a standard practice for most haulers, and for more than a decade Impact Environmental Group (IEG) has been supplying the most cost-efficient way to do this via prefabricated steel bottoms.

In 2021, IEG set out to develop a more permanent solution to replacing rusted container bottoms by leveraging both its metal fabrication and plastic forming core capabilities. “Our research showed that a container averages about three replacement bottoms over its life,” says Brian Beth, president and CEO of IEG. “So, we were intrigued by the idea of eliminating bottom corrosion after just one replacement or, even better, being incorporated into a new container.”
This was the genesis of the Dura-Bottom Container Repair System, a high-density polyethylene plastic bottom that will never rust or corrode and is bolted to a container using a coated metal flange. The Dura-Bottom was designed to eliminate multiple bottom replacements, lowering the total cost of container ownership and reducing the associated impact to the environment. In addition, the flange system provides standardization, allowing 8 SKUs to cover almost all front-end-load (FEL) container sizes.
Excited about the concept, IEG brought the first prototype of the Dura-Bottom to the 2021 WasteExpo, and it became one of the highlights of the show.
-web.gif)
“When you get that type of feedback on a new concept, I think it’s natural to want to rush the product to market,” says Paul Reidy, vice president of Marketing for IEG. “But we are fortunate to have seasoned product development people on our team who have seen the pitfalls of falling in love with a concept before proving it out in the field.”
After Waste Expo, IEG sought to ensure the Dura-Bottom could withstand the use and abuse a steel container experiences in the field. IEG built production molds and set out on a yearlong beta test that involved partnering with haulers to put Dura-Bottoms into the field, specifically targeting harsh environments and regions that experience a high volume of bottom replacements. The Dura-Bottom has proven to be successful, holding up to weekly dumping, saltwater exposure, high humidity and locations with liquid and organic waste.
In January, IEG officially launched the Dura-Bottom Container Repair System.
“After a long period of beta testing, we were confident that the product met the promise and are excited to make it available to the market,” Beth says.
Latest from Waste Today
- US Composting Council grant will fund data collection
- Enviri releases annual ESG report
- Waste Connections enjoys income, revenue boosts
- Machinex recognized as Recycling Equipment Innovator of the year
- WM announces solid Q2 growth
- Reworld partners with Genpact
- Waste Pro earns favorable financing rating
- Amberjack announces exit from investment in Best Trash