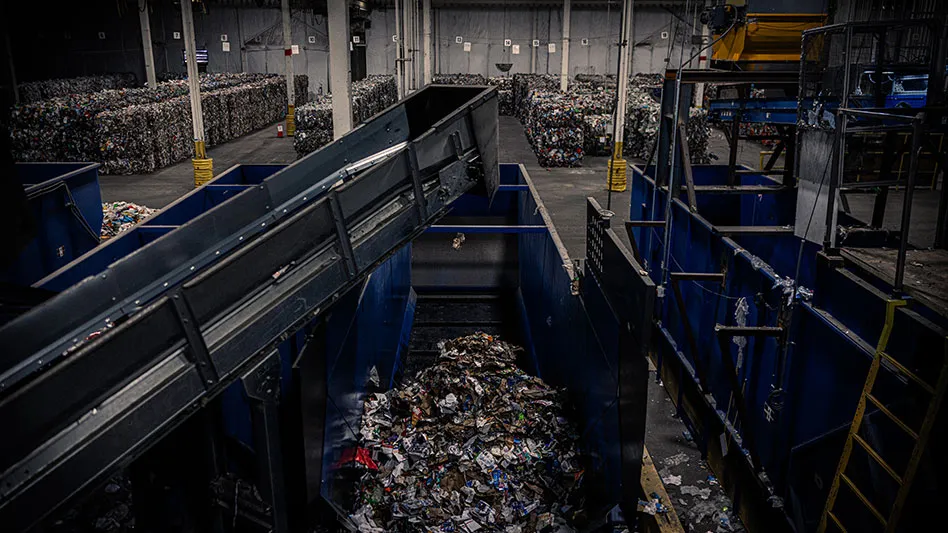
Photo courtesy of Amp
Amp Robotics has rebranded as Amp and launched a new website to better reflect the evolution of the business from a provider of artificial intelligence (AI) and robotics to fully automated, facility-scale sorting solutions that integrate its AI-powered sorting technology.
Amp CEO Matanya Horowitz tells Recycling Today the company has been working on applying AI in the recycling industry for some time, and that robots were one main way to take advantage of that technology.
Since its founding, Amp has introduced a variety of AI-enabled technology, from the Cortex-C, a compact version of its robotics system, to Vortex, which targets and recovers film and flexible packaging. These solutions often were designed to be retrofitted into facilities. However, the company’s new Amp One consists of a set of different tools the company can apply to greenfield projects rather than retrofits, providing “a high certainty that recovery rates are optimized,” Horowitz says.
He adds that Amp realized it could have a greater impact building greenfield facilities as opposed to retrofitting AI-enable robots into preexisting facilities.
“We started changing how we talked about our solutions and the future of the company,” Horowitz says. “We were talking and thinking about things differently; branding is a way to communicate those things.”
He says the company has been broadening its language and the people it’s talking with to include stakeholders not just at the material recovery facility (MRF) level but also landfill operators, consumer packaged goods companies, petrochemical companies and municipalities to address waste flows in an entire region. These stakeholders often were “talking past one another and not understanding with the other counterparty needs,” he says, though it was clear to Amp that sorting is the core issue all these stakeholders share.
In a Feb. 1 blog post announcing the change, Horowitz writes, “We’re selling more than robots—we’re providing solutions that address the waste industry’s biggest challenges, and we’re ready to introduce a new brand identity that reflects our delivery of AI-powered sortation at scale."
The company’s facility-scale sorting solution, Amp One is based on its secondary sorting facilities and “capitalizes on the experience we’ve gained developing best-in-class recycling technology and brings it together in a way that’ll allow us, and the industry, to realize the tremendous opportunity in sortation at scale,” Horowitz writes. “We serve an industry that does a hard job—one that’s seldom celebrated and never done. Our technology enables the waste industry to harness the power of AI to do this hard job better, faster and more efficiently.”
With Amp One, the company is focused on reducing labor costs, increasing resource recovery, increasing landfill diversion and ensuring more reliable operations.
Amp One refers to a suite of different solutions, including Jet, the high-efficiency sorting technology that is the company’s answer to optical sorters. Amp Jet uses the same core concepts of optical sorters in that it employs puffs of air to separate materials, but the company’s technology can be used on tilted conveyor belts, eliminating the need for large vertical gaps in processing systems, Horowitz says, allowing Amp to make facilities less vertical and more compact and easier to maintain.
Amp Jet also does not use infrared or hyperspectral imaging but only AI as well as air nozzles of different strengths. Horowitz says those changes mean the technology also can be deployed on the presort. The company also uses AI to watch the flight path of material, enabling ongoing improvements. He adds that Amp Jet avoids the calibration and maintenance issues associated with traditional optical sorters.
Other technologies, such as the Delta, a robotic sorter, and the Vac film sorter use AI and can provide a comprehensive waste characterization at every spot in the line, Horowitz says.
Proactive monitoring means the system “asks for help where needed,” he says, and provides better uptime than traditional sorting systems.
By varying how the equipment in Amp One is arranged, Horowitz says, the company can remove traditional screening technology and create compact container lines.
He says Amp One can be thought of as architectural building blocks that can be applied to single-stream, secondary and dirty MRFs.
“We have a heavy focus on recirculating material,” Horowitz says of Amp One. “We can be very careful about the quality if we let a little more material go by. That is part of our core design. The system watches and sees what is circulating and keeps track of contamination.”
Once all the recyclables have been recovered, the system automatically purges before loading additional material. While the system can operate without manual sorters, depending on the material stream, Horowitz says human intervention is needed for maintenance and to address jams.
With Amp One, the company uses the same approach to data as it has with its robots, he says, and the same nondisclosure and confidentiality agreements apply. “The operator has all the data and can use it however they like. We still need to pull this data ourselves to improve the technology,” he says, noting that machine learning is occurring at multiple levels as well as at the system level. “The system as a whole is capable of learning.
“We really want to ensure the success of these projects. I love our robots—our robots are incredible—but they were held back by overworked maintenance workers.” That is why Amp is assigning a highly technical account manager to work with facilities that use Amp One to create a “high level of partnership” to ensure adequate maintenance, he says.
Latest from Waste Today
- US Composting Council grant will fund data collection
- Enviri releases annual ESG report
- Waste Connections enjoys income, revenue boosts
- Machinex recognized as Recycling Equipment Innovator of the year
- WM announces solid Q2 growth
- Reworld partners with Genpact
- Waste Pro earns favorable financing rating
- Amberjack announces exit from investment in Best Trash